在冶金钢铁行业中,回转窑是一种至关重要的核心设备,其独特的工作原理为钢铁的生产过程提供了关键的支持。深入了解回转窑的工作原理,对于优化生产工艺、提高生产效率以及保证产品质量都具有重要意义。
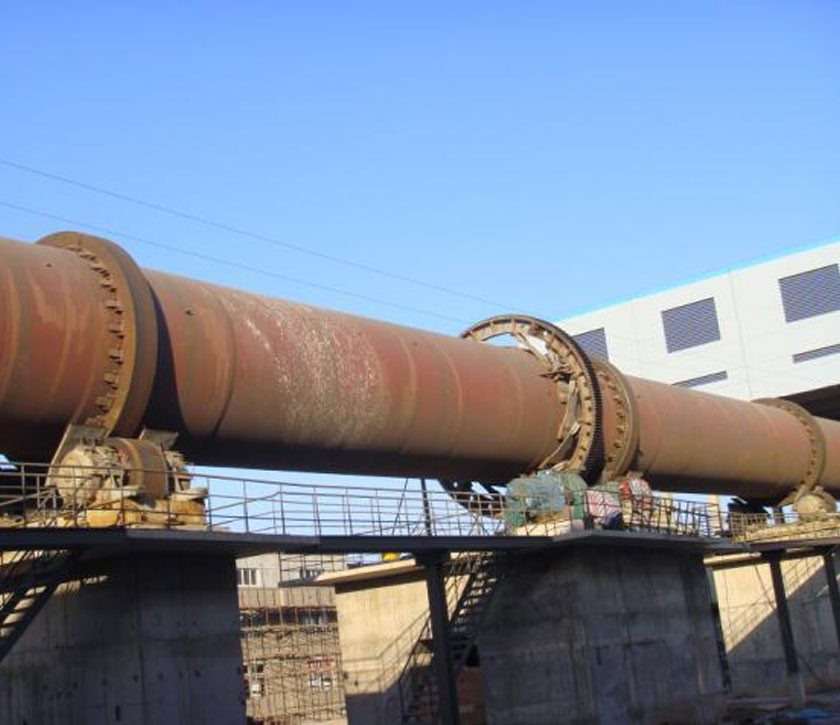
一、回转窑的基本结构
冶金钢铁回转窑主要由筒体、传动装置、支承装置、密封装置以及窑头和窑尾等部分组成。筒体是回转窑的主体部分,通常由耐高温、耐磨的钢材制成,内部衬有耐火材料,以承受高温和物料的磨损。传动装置负责驱动筒体旋转,一般采用电机通过减速机带动筒体上的大齿圈转动,使筒体以一定的转速匀速旋转。支承装置用于支撑筒体,并保证其在旋转过程中的稳定性,通常包括轮带、托轮等部件。密封装置则设置在窑头和窑尾,防止空气进入或物料泄漏,以维持窑内的热工制度和生产环境。
二、物料在回转窑内的运动过程
1.进料端
待处理的物料(如铁矿石、石灰石、焦炭等)通过特定的进料装置进入回转窑的窑尾部分。在窑尾,物料由于筒体的倾斜和旋转作用,开始向窑头方向缓慢移动。此时,物料处于相对松散的状态,随着筒体的转动逐渐被带起并在一定高度落下,形成物料的 “滚落” 运动。
2.筒体内部运动
当物料随着筒体的旋转不断向窑头移动时,其运动方式变得更加复杂。一方面,物料在筒体的旋转带动下继续做 “滚落” 运动,不断地被提升和落下,使得物料在窑内能够充分混合和翻动。这种翻动有助于物料均匀受热,促进化学反应的进行。另一方面,物料还会沿着筒体的轴向向前移动,其移动速度受到筒体转速、倾斜角度、物料性质等多种因素的影响。一般来说,通过调整筒体的转速和倾斜度,可以控制物料在窑内的停留时间,以满足不同的生产工艺要求。
3.出料端
经过在窑内一系列的物理和化学变化后,物料到达回转窑的窑头部分。在窑头,经过处理的物料通过出料装置排出窑外,进入后续的工艺流程,如冷却、筛分、冶炼等环节。
三、热量传递与反应过程
1.燃烧与热量产生
在回转窑的窑头部分,通常设置有燃烧器,用于燃烧燃料(如煤粉、天然气等)。燃料燃烧产生的高温火焰和热气向窑内喷射,为物料的加热和反应提供热量。燃烧产生的热量以辐射、对流和传导等方式传递给窑内的物料和筒体。
辐射传热是主要的热量传递方式之一,高温火焰和窑壁向物料辐射热量,使物料表面吸收热量并温度升高。对流传热则是通过热气与物料之间的相对流动,将热量传递给物料。同时,热量也会通过筒体的传导作用,从窑壁传递到物料内部,使得物料整体受热均匀。
2.物料的加热与反应
随着物料在窑内的移动和受热,一系列的物理和化学变化相继发生。例如,在铁矿石的焙烧过程中,物料首先被加热脱水,去除其中的水分。随着温度的进一步升高,铁矿石中的一些矿物质会发生分解和氧化反应,生成新的化合物。在石灰石的煅烧过程中,石灰石会分解成氧化钙和二氧化碳,这个过程需要吸收大量的热量。这些反应在回转窑内特定的温度、气氛和停留时间条件下进行,通过精 确控制这些参数,可以实现预期的生产目标和产品质量要求。
3.热平衡与温度控制
为了保证回转窑内的热量传递和反应过程稳定进行,需要维持窑内的热平衡。这涉及到对燃料的供给量、空气的摄入量、物料的流量以及窑体的散热等因素的综合调控。通过安装在窑内不同位置的温度传感器,可以实时监测窑内的温度分布情况。根据监测数据,调整燃烧器的燃料供应和空气配比,以及筒体的转速等参数,以确保窑内各区域的温度保持在合适的范围内,满足物料反应的需要。
四、气体流动与排放
1.燃烧废气的产生与流动
燃料燃烧后会产生大量的燃烧废气,主要成分包括二氧化碳、氮气、水蒸气以及少量的二氧化硫、氮氧化物等污染物。这些废气在窑内随着热气的流动向窑尾方向移动。由于窑内存在一定的压力差,废气会在窑尾通过专门的废气排放装置排出窑外。
2.气体的循环利用与环保处理
在一些先进的冶金钢铁生产工艺中,会对部分燃烧废气进行循环利用。例如,将废气中的余热回收用于预热空气或物料,以提高能源利用效率。同时,对于废气中的污染物,需要经过严格的环保处理,如采用脱硫、脱硝设备等,减少对环境的污染。在窑内,合理的气体流动控制还可以影响物料的反应气氛和传热效果。通过调整通风量和气体流速,可以调节窑内的氧气含量和压力分布,为物料的反应创造适宜的条件。
冶金钢铁回转窑的工作原理是一个复杂而又精细的过程,涉及物料的运动、热量的传递、化学反应以及气体的流动等多个方面。通过深入理解和掌握这些原理,并不断进行技术创新和优化,能够使回转窑在冶金钢铁生产中发挥更加高效、稳定和环保的作用,为钢铁行业的发展提供坚实的支撑。